7 Strategies For Improving The Reverse Logistics Process
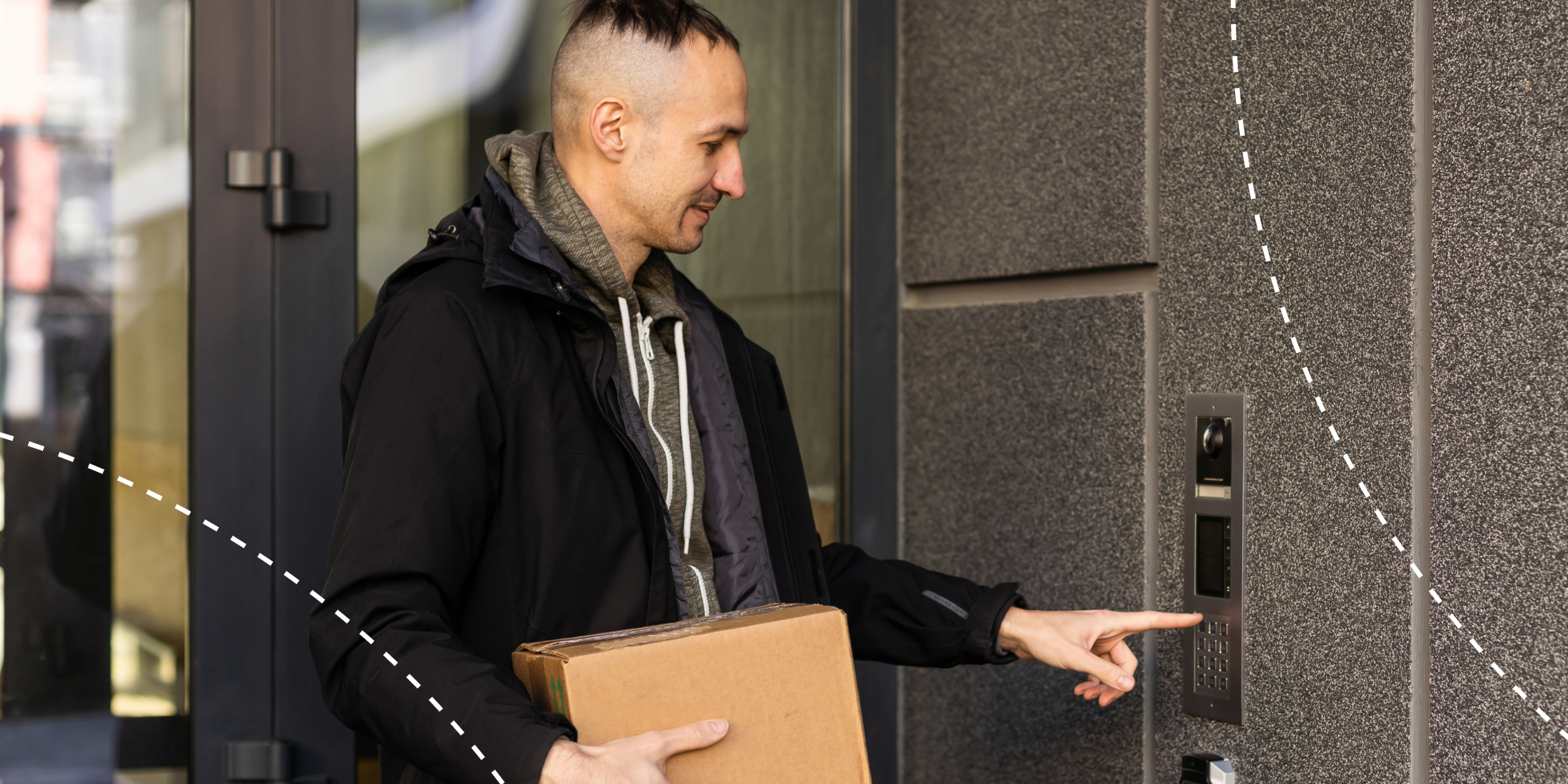
The reverse logistics process, a linchpin of modern supply chain operations, particularly in the realm of online retailing, has a profound impact on business operations. Reverse logistics refers to the process of managing the movement of goods from their final destination back to the manufacturer or retailer, handling returned items, and implementing strategies to reduce costs and losses related to returns.
It enables businesses to offer customers the reassurance of product returns in the face of challenges or issues, thereby boosting customer satisfaction and trust, while opening up opportunities for businesses to enter the recommerce industry. Optimized reverse logistics in managing product returns can lead to significant bottom line benefits, reduce environmental impact, enhance customer retention, and improve supply chain visibility. The reverse logistics process is a permanent fixture in modern supply chain management, with experts predicting it will evolve into a trillion-dollar market in a few years.
However, if the system is more of a necessity than an option, then it becomes imperative for more supply chains and businesses to prioritize investing in optimizing or improving it for greater success.
In this article, we explore key strategies that these businesses and supply chains can adopt to successfully improve their reverse logistics process, thereby improving the throughput of the entire operation. So, what are these strategies?
1. Implement a Customer-Centric Returns Policy
Return policies play a key role in educating customers about what to expect from the reverse logistics and returns management process. Each business and supply chain may have its own unique returns policy, but they must all be customer-centric. This approach not only ensures that the customers feel valued and supported but also leads to increased customer loyalty and satisfaction.
For instance, a customer-centric return policy is easy to find, understand, and navigate, making the return process a breeze for the customers. Implementing a customer-centric returns policy is key for driving sales, especially when additional incentives, such as free returns, can boost sales by over 350%. In a competitive economy where the customers hold all the cards, a customer-centric returns policy operates as a game changer, enhancing customer satisfaction.
Beyond tweaking the return policy to be user-friendly to the customers, more supply chains must ensure that the entire reverse logistics process, including the returns management, is tweaked to meet the promises made to customers. For instance, if the returns policy offers multiple options, the supply chain must ensure it can deliver on all those. Failing to fulfill promises negatively affects the customer’s perception of the business. More importantly, it could derail sales.
2. Leverage Technology
Technology is the backbone of modern supply chain operations. In an increasingly interconnected world, technology enhances the ability of supply chains to constantly adapt and meet customer demands. Technology solutions have significantly allowed businesses to optimize these processes, from inventory management to warehousing operations, procurement, and traditional logistics management. The same can apply to reverse logistics management.
Through technology, robust solutions like the returns management system exist and allow more retailers and their supply chains to streamline the entire reverse logistics operation through automation. These typically include processing returns, sorting, and inventory management. Technology solutions or applications like the RMS optimize the reverse supply chain, allowing for speeding up the entire process while reducing errors.
Technology solutions like the returns portal allow customers to navigate the returns management process easily. Through these portals, they can activate returns, get approval, generate return labels, and track the entire process.
3. Streamline The Returns Management Process
The returns management process must be easy for customers and the team working on the backend of the returns processing to follow. This way, the supply chain can save time and enhance the throughput of the entire process. For instance, the returns process must have minimal steps on the customer’s end to ensure a seamless experience.
The processing team should have dedicated return centers for handling returns, and the entire process must be centralized. These two will enhance the efficiency and consistency of the process and improve the turnaround time. A streamlined returns management process saves cost, reduces waste, and empowers the supply chain to quickly spot fraudulent returns.
4. Enhance Inventory Management
The success of the reverse logistics process will, to a great extent, be tied to the supply chain’s ability to integrate the items back into the supply chain as easily as possible. For instance, a customer is returning a blue cup because she thought it was pink when she ordered it. If the business had a stock of 9 blue cups, would this return mean they now have 10 cups? Do they still have 9 cups?
What if another customer orders 10 blue cups? What does the business or supply chain do here? The answer lies in streamlining the inventory management operation, where products to and from the supply chain are constantly being monitored in order to have an overall and precise picture of the inventory on hand. This allows for better planning and decision-making.
5. Improve Communication Between Customers and Stakeholders
The entire reverse logistics operation will struggle without proper communication, especially with the stakeholders and customers involved. Communication brings balance to the supply chain and enhances visibility and transparency across the entire process. Communication with stakeholders streamlines the processes in the reverse logistics operation, allowing for proactive steps, including pick-up and delivery.
On the other hand, communication with customers ensures they are kept in the loop every step of the way. Although customers generally want faster logistics, they prefer staying in the loop, even when there are delays. This level of transparency can improve customer satisfaction significantly. Through effective and proactive communication, the business can establish a customer feedback loop, which they can leverage to understand the customer’s issues and improve the returns process based on their output.
6. Partner With a Third Party Logistics Partner
Modern supply chains are much more complex than ever, and to successfully manage them, more businesses are collaborating with experts in the various aspects of the supply chain operation. One of these is the reverse logistics process. The supply chain can easily optimize the entire reverse logistics and returns management process with a third-party reverse logistics provider.
These third-party logistics providers leverage their expertise, vast resources, and experience to improve the throughput of the process, allowing the business and supply chain to focus more on core aspects of the operation. However, partnering with these providers successfully will necessitate trust, integration, and seamless communication.
7. Focus on Sustainability
Logistics and transportation (including the reverse logistics process) generally amount to a significant portion of greenhouse gas emissions. By focusing on sustainability, including reevaluating waste protocols and leveraging technology solutions like TMS and RMS, more supply chains can reduce these emissions by merging the delivery and pick-up process and then thoroughly sorting the returned goods to ensure zero unnecessary waste.
How ReverseLogix Improves Your Reverse Logistics
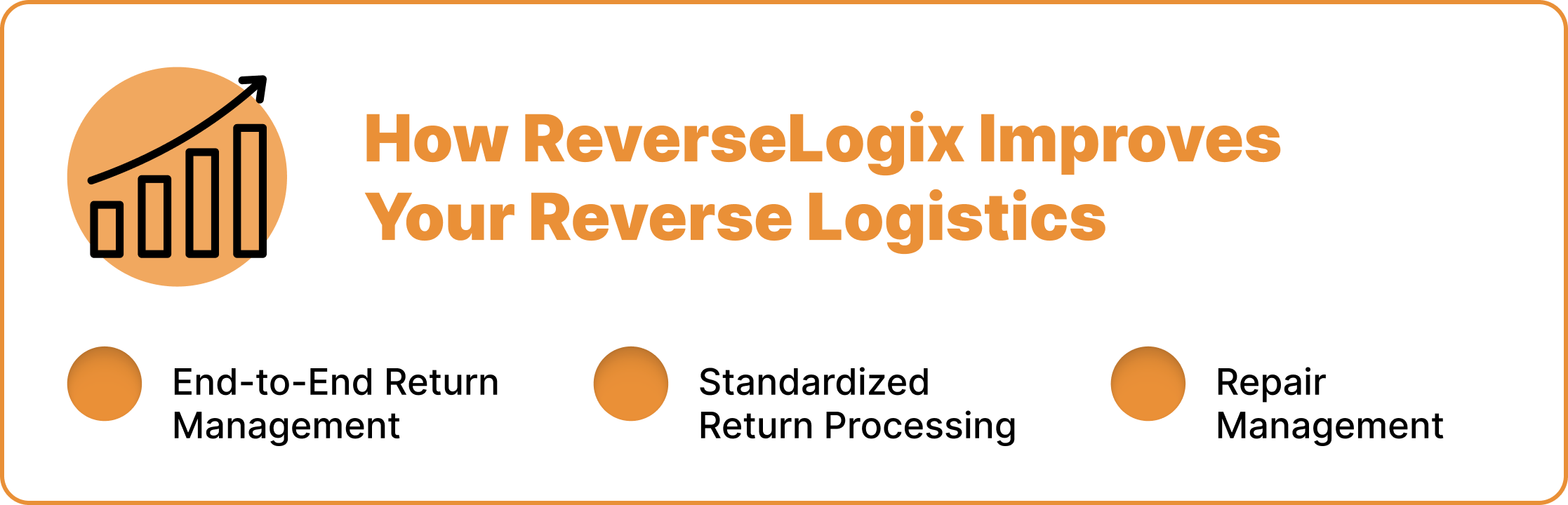
ReverseLogix offers a comprehensive solution for managing complex returns, allowing businesses to initiate returns, configure processing, and handle repairs within a single system. With ReverseLogix, you can expect the following:
- End-to-End Return Management: Customers can initiate returns through a self-service portal integrated with existing systems, maintaining visibility and control.
- Standardized Return Processing: Set up workflows for verifying, inspecting, and grading returns to maximize recovery.
- Repair Management: Use guided workflows to identify and repair products, recouping costs from damaged items.
Connect with us today and feel the difference.
Frequently Asked Questions
An effective reverse logistics system allows supply chains to enhance customer satisfaction, reduce costs of operation while increasing efficiency, and then contribute to sustainability by promoting recycling and proper disposal of products.
Reverse logistics can be subject to several challenges, depending on the industry, the nature of the business, and the set-up of the supply chain management. However, some of the common challenges many businesses experience in their reverse logistics operation are high return rates, inefficient processes, lack of visibility, manual handling errors, high transportation costs, and complex product assessments.
Data analytics is a critical aspect of improving reverse logistics and returns management processes because it helps identify trends, predict return volumes, optimize inventory management, and improve decision-making by providing insights into the reverse logistics process. This data is generally obtained by creating a feedback loop and system.
Supply chains can standardize their reverse logistics processes by any number of processes but the following are typical: creating uniform policies, procedures, and workflows for handling returns, repairs, and recycling, ensuring consistency and efficiency of their forward logistics process.